Could ERP Efficiencies Be Hiding in Plain Sight?
- MSSBTA
- Oct 28, 2021
- 1 min read
Updated: Nov 11, 2021
Many organizations implementing ERP drive hard to go-live, but once the system is up and running, they fail to optimize for the changing business environment. Where they could utilize ERP efficiencies within the system, they are ultimately leaving money on the table.
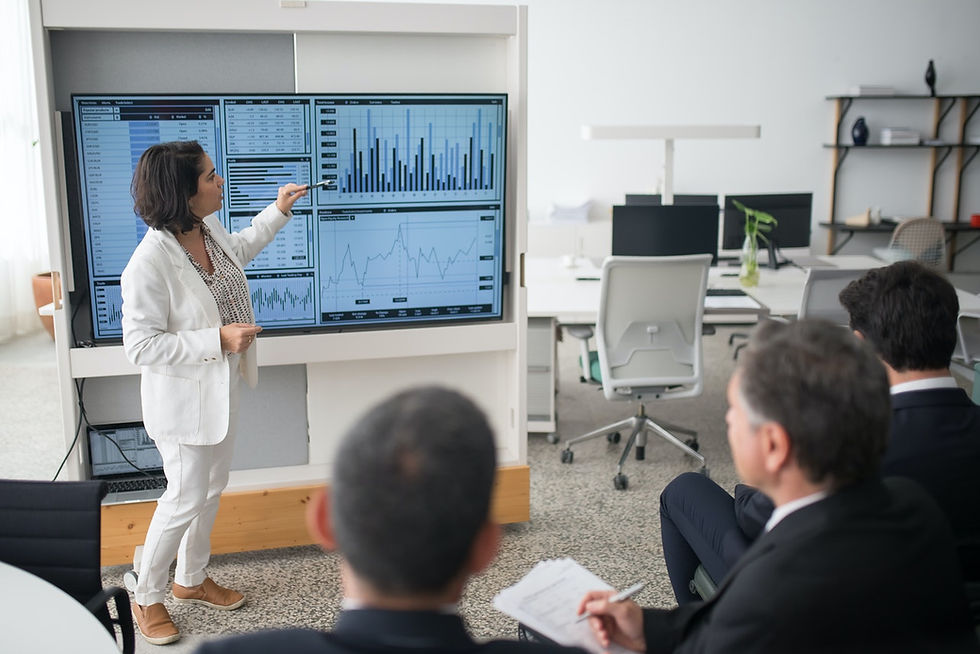
ERP Efficiencies Commonly Missed
Automated bank transactions warehouse
Automated inter-company sales
Budget checking on PO’s (tightly controlled encumbrance process for grant tracking)
Landed cost linked to inventory through manufacturing to get true costing
Automated cash receipts / lockbox processing
In addition to the above, consider if your organization is making the most of the functionality available in the modules you own. For example, in the Purchasing module, are Approvals being utilized fully and successfully? Are Purchase Requisitions and/or Purchase Quotes used most efficiently?
In another article, 8 Differences Between a Common ERP Approach and an Optimized One we discussed the example of a user interface that hadn’t changed since the initial implementation. As a result, it looked “old school” and didn’t offer the experience users were used to with other systems. By simply implementing other available versions of screens for ease-of-use, they could have easily changed processing options or data selections making data entry faster and easier, thereby increasing productivity.
Improve Overall Operations
By uncovering efficiencies already available in your ERP system your organization could be just steps away from realizing company-wide benefits that optimization brings and avoid leaving money on the table.
Uncover and implement new hidden efficiencies by:
Meeting with your ERP end users to identify usage and/or training gaps
Assessing your ERP environment with a focus on improving efficiencies via setup/ technology/reporting
Providing ERP documentation comparing your current system to the latest releases of the application
Comments