Maximizing Efficiency Through Practical Performance Optimization
- Faouzi Charfadi
- Feb 14
- 2 min read
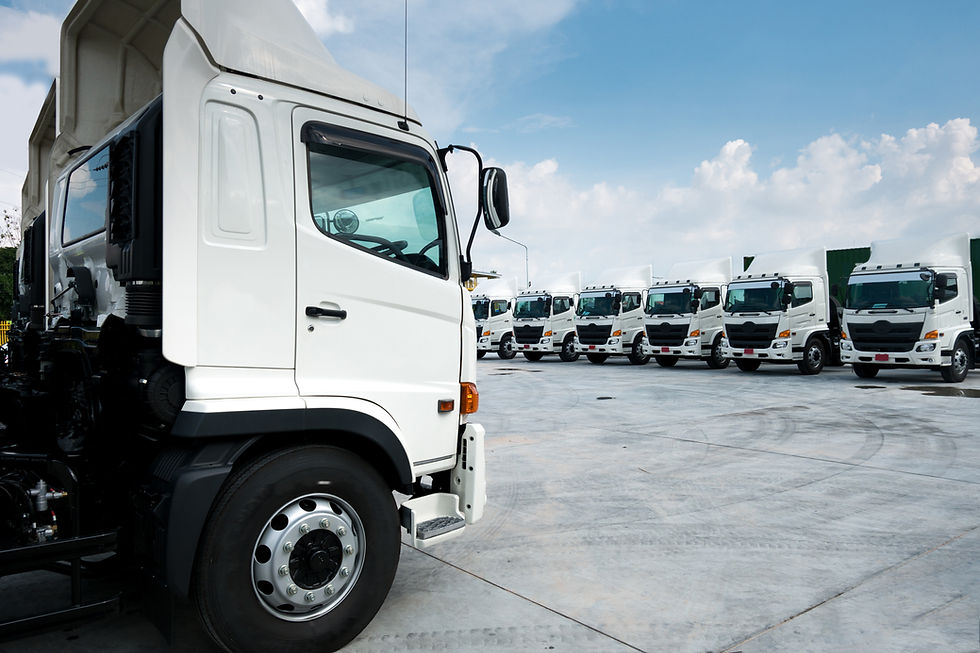
Performance optimization is a continuous process that involves measuring performance, identifying bottlenecks, implementing improvements, and reassessing the results. It is a matter of applying logical, effective techniques tailored to a system’s specific needs. The goal is to enhance efficiency, speed, and overall user experience.
One of my clients operates a delivery company with twenty-five locations across the U.S. Each location manages an average of thirty trucks, mostly 17-foot trucks, along with three 26-foot bulk trucks equipped with liftgates. Each bulk truck requires both a driver and a helper.
During a visit to my client’s Los Angeles location, I observed that, despite business growth, workplace injuries were negatively impacting productivity and profitability. After receiving permission to analyze the operation for a few days, I gathered insights and presented my findings. The primary issue stemmed from the physical strain placed on workers who had to manually push or pull pallets weighing anywhere from a few hundred to two thousand pounds, especially in the hilly Los Angeles terrain.
When my client inquired about implementing a Lean Six Sigma project to address the issue, I assured him that a simpler, more immediate solution was available. Data analysis confirmed the potential for a significant efficiency boost and cost reduction.
Each bulk truck employs both a driver and a helper. The driver earns an average annual salary of $60,000, while the helper earns $48,000, totaling $108,000 in labor costs per truck per year. With three bulk trucks per location across twenty-five locations, the total labor cost reached $8,100,000 annually.
By replacing the helper with an electric forklift, we drastically reduced costs. The initial cost of the forklift was $10,000, with an annual maintenance cost of $1,000. In the first year, this reduced the per-truck operating cost to $71,000, resulting in a $37,000 saving per bulk truck.
With seventy-five bulk trucks in operation, the annual savings amounted to $2,775,000, excluding additional benefits from reduced workplace injuries. The use of electric forklifts significantly decreased the risk of strain-related injuries, as drivers no longer needed to push or pull heavy pallets. The long-term savings were even great if my client retained each forklift for three years, an additional $75,000 per truck would be saved in years two and three.
The client was thrilled with the results. Instead of layoffs, the helpers were reassigned as solo drivers or warehouse loaders, improving overall operational efficiency. By implementing this straightforward performance optimization strategy, we reduced costs, increased efficiency, and improved workplace safety—without the need for an extensive Lean Six Sigma project.
At MSSBTA, we specialize in helping businesses operate more efficiently, reduce costs, and gain a fresh perspective on their operations. Your success is our priority.
Comments